2025-06-16 Closed recycling loop for Infinity press felts from Voith reduces specific carbon footprint by up to 31 percent
- Infinity +Green press felts, developed for recycling and produced sustainably, reduce the product's carbon footprint by 15 percent
- Closed recycling loop reduces the product's carbon footprint by an additional 16 percent
- Innovative method enables unlimited recycling cycles without compromising quality
HEIDENHEIM, GERMANY. Voith, leading full-line supplier of solutions to the paper industry, is launching an innovative recycling concept for press felts in collaboration with its partner Aquafil, enabling papermakers to drastically reduce their specific product carbon footprint. The newly developed Infinity +Green press felts and a closed recycling loop reduce Scope 3 emissions by up to 31 percent.
“Design for Recycling” concept
Voith's Infinity +Green press felts have been specially developed for recycling, with particular attention to the homogeneity of the product. Thanks to the implementation of the “Design for Recycling” concept, only one type of polyamide is used in the production of Infinity +Green. In order to meet the high-quality requirements of paper machine fabrics, Voith relies on chemical recycling through depolymerization. To this end, Voith works closely with Aquafil, a pioneer in PA 6 recycling. In this process, used PA 6 is converted into the monomer caprolactam, which is efficiently purified and repolymerized into high-quality PA 6 granulate under the brand name ECONYL. Depolymerization has proven to be less energy-intensive than other chemical recycling methods. In addition, this process preserves the original material quality, as unlike mechanical recycling, there is no loss of quality due to downcycling.
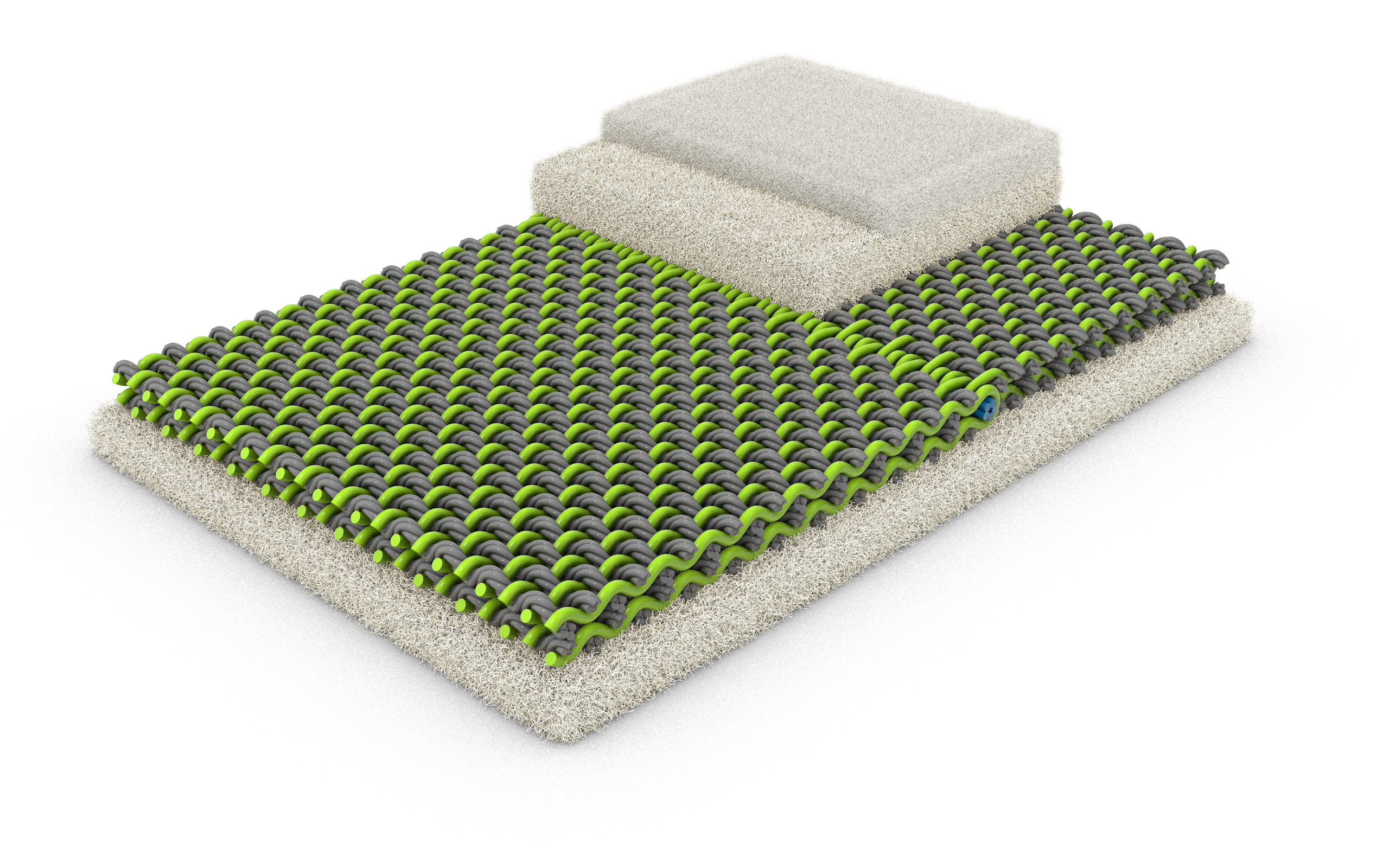
Reuse of resources in low-emission production
Voith uses recycled ECONYL granulate from Aquafil to produce new material for press felts at its own site, which perform exactly the same as felts made from new material. For felt production, Voith uses only green electricity, which is partly generated by the company's own hydropower plant. Thanks to the forward-looking design and sustainable production methods, papermakers using Infinity +Green benefit from a 15 percent reduction in Scope 3 emissions compared to conventional press felts.
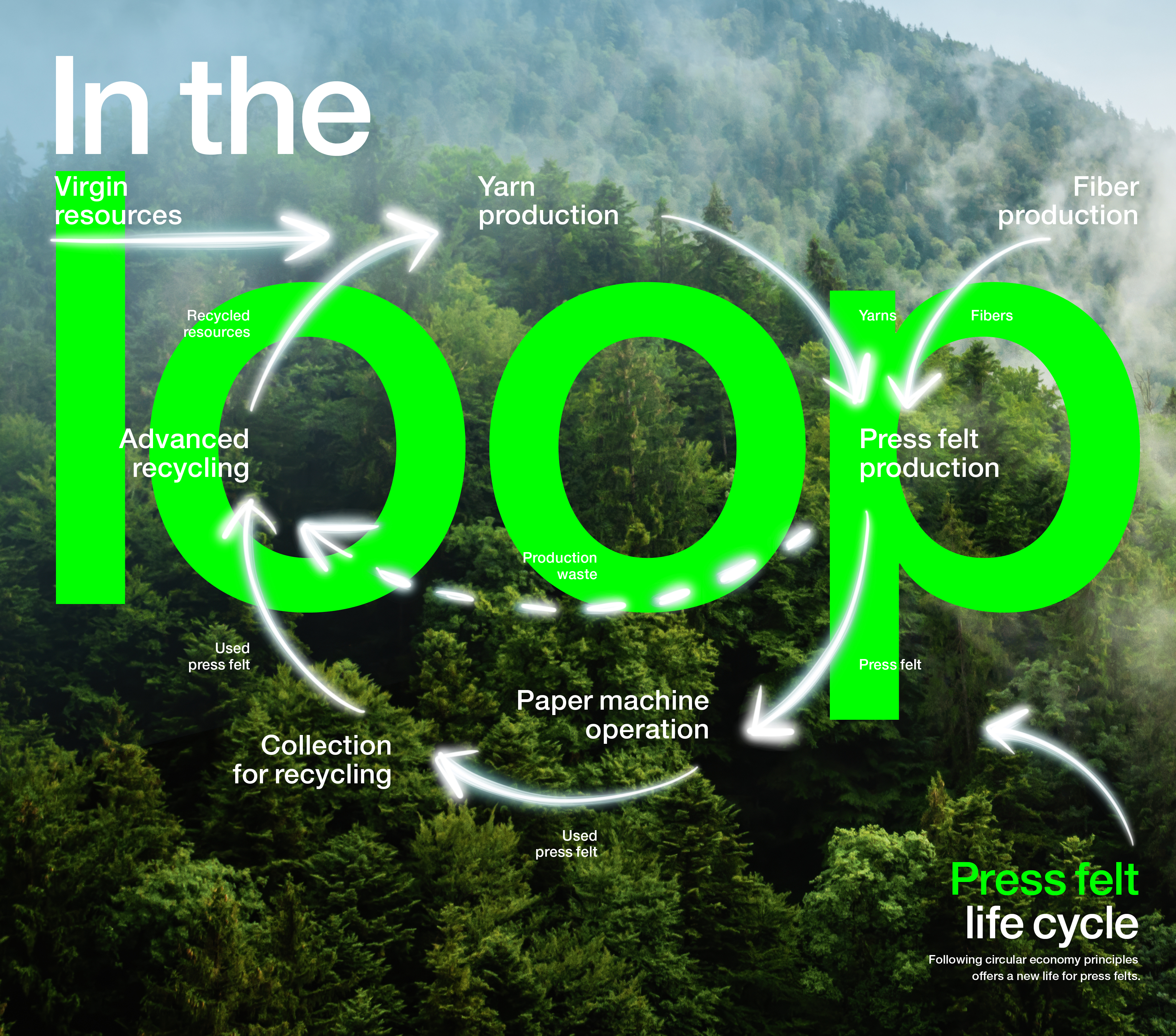
Closed loop ensures a further 16 percent reduction in emissions
A closed recycling concept reduces the product's carbon footprint by a further 16 percent. This way, used press felts from papermakers and unavoidable production waste are turned into new, high-performance press felts.
The new Infinity +Green press felts are compatible with any machine configuration. Infinity +Green is already available everywhere in the EMEA region, with plans to expand global availability. With Infinity +Green press felts, Voith has achieved a breakthrough in the product-to-product recycling process. The latest advances underscore the leading full-line supplier's commitment to a sustainable future and its claim to support papermakers in achieving their ambitious sustainability goals.
About the company
The Voith Group is a global technology company. With its broad portfolio of systems, products, services and digital applications, Voith sets standards in the markets of energy, paper, raw materials and transport & automotive. Founded in 1867, the company today has around 22,000 employees, sales of € 5.2 billion and locations in over 60 countries worldwide and is thus one of the larger family-owned companies in Europe.
read more
The Group Division Voith Paper is part of the Voith Group. As the full-line supplier to the paper industry, it provides the largest range of technologies, services and products on the market and offers paper manufacturers holistic solutions from one source. The company’s continuous stream of innovations facilitates resource-conserving production and helps customers minimize their carbon footprint. With its leading automation products and digitalization solutions from the Papermaking 4.0 portfolio, Voith offers its customers state-of-the-art digital technologies to improve plant availability and efficiency for all sections of the production process.